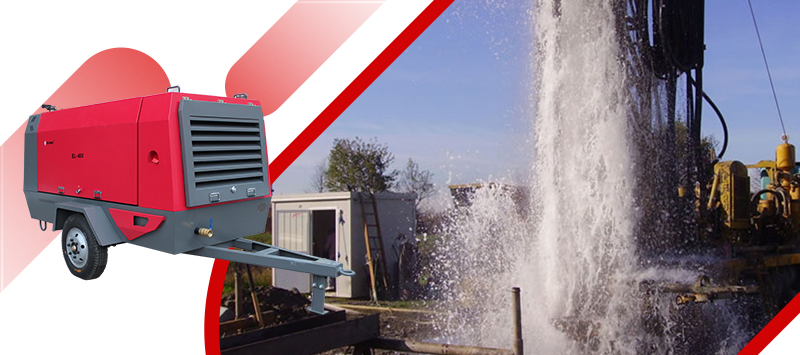
Water accounts for a considerable proportion in the human body, accounting for approximately 60% to 70% of its volume. It plays a crucial role in maintaining cell vitality and the normal operation of various organs. In fact, water is crucial for vital functions such as cell metabolism, nutrient transport, waste removal, and body temperature regulation. It can be said that water is the cornerstone of our lives. If the loss of water in the body reaches more than 20%, it will lead to severe dehydration and even endanger life.
Throughout history, humans have obtained this precious resource through various means. In addition to collecting rainwater and utilizing lakes, well water has been a major source of water. Groundwater is not only a renewable natural resource, but it is also relatively clean, helping to prevent water contamination. This makes it an important resource in areas where other water sources are difficult to access. In recent years, advancements in drilling technology have allowed for the extraction of water from wells, providing clean water sources to a wider population.
In this context, diesel mobile air compressors play a crucial role in the drilling process. Its advantage is that it can be adjusted according to actual needs at any time, meeting various temporary air needs, providing necessary power and support for drilling operations, and further ensuring the acquisition of water resources. Diesel mobile air compressors efficiently compress air to provide stable high-pressure air for drilling operations.
What is the use of air compressor in drilling?
1. It allows for better control and precision during drilling operations. By adjusting the air pressure, operators can fine-tune the drilling speed and depth, ensuring optimal performance and minimizing the risk of errors.
2. Optimizing compressed air pressure reduces wear and tear on drilling equipment. When the pressure is too high, it can bring unnecessary pressure to the tool, leading to premature wear and increased maintenance costs. On the other hand, if the pressure is too low, drilling efficiency can be affected, resulting in longer drilling times and potential equipment failures.
3. Optimizing compressed air pressure contributes to energy efficiency. The use of appropriate pressure can minimize energy waste and reduce operating costs. By knowing the best pressure requirements for your particular drilling application, you can ensure that your compressor runs at maximum efficiency, saving money and resources.
What pressure of compressed air should be applied to a drill?
In the work of drilling wells, the pressure of the air compressor needs to be adjusted to an appropriate range. The pressure requirement is different because of different geological environment and well depth. Air compressors have multiple pressure levels, with the maximum working pressure typically ranging from 1.75 to 2.45 MPa. In normal circumstances, this working pressure is sufficient for air drilling. However, in practical operations, adjustments need to be made based on factors such as well depth, rock type, and geological environment to better adapt to different working conditions. Additionally, the appropriate pressure range needs to be determined based on the material and hardness of the drill bit. When drilling at greater depths or when encountering anticipated water inflow, the required air pressure for delivery may exceed the rated pressure of the air compressor, requiring the use of an air booster.
What are the common mistakes to avoid with drilling air compressors?
1. Neglect the regular maintenance and inspection of the compressor. Over time, dirt, debris, and pollutants can accumulate, leading to reduced efficiency and potential failure. By implementing a comprehensive maintenance plan, you can keep the compressor in optimal condition and prevent unnecessary downtime.
2. The compressor is overloaded. Every compressor has its limits, and exceeding these limits can lead to performance degradation and potential damage. Always ensure that your drilling operations comply with compressor specifications and capabilities.
3. Failure to properly train and educate operators on the optimal use of compressors can lead to inefficiency and errors.
Daily maintenance for drilling air compressors
1. Replace oil regularly as recommended by the manufacturer to keep the engine lubricated and prevent wear and tear. Check oil level and quality regularly, especially before each operation.
2. Regularly inspect and clean or replace air filters to prevent dust and debris from entering the engine and to maintain airflow stability.
3. Check the fuel system for leaks and make sure the fuel line and filter are in good condition. Regularly remove water from fuel filters to prevent contamination.
4. Check drive belts and hoses for signs of wear, cracking or damage and replace any damaged parts immediately.
5. Check the cleanliness of the cooling system and check for any debris; check the level and quality of the coolant and replace as needed.
6. Change fuel and oil filter regularly to keep fuel and oil clean.
7. Check the status of battery and electrical connection, clean and tighten if necessary.
8. Check the level of engine coolant, hydraulic oil and other oil regularly to keep working normally.
9. Ensure that the safety shutdown system of the diesel Air compressor works properly and is responsive to any problems.
10. Check the normal operation of the safety valve to prevent over-pressure.
11. Record all maintenance activities, including filter replacement, oil replacement and inspection.
12. Always follow the manufacturer’s maintenance schedule and user manual guidelines.
13. In the need for major maintenance or repair, you can consider hiring professional and technical personnel to repair the compressor.