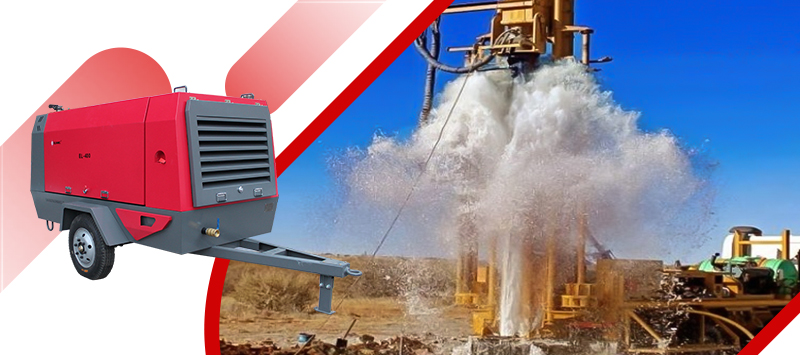
The water well drilling industry plays a vital role in providing access to clean and sustainable water sources. The drilling process involves various complex tasks, and one crucial piece of equipment that is indispensable in this industry is the air compressor.
Water well drilling structure
1.Hydraulic oil pump
It is a double-type high-capacity pump that provides power for the power head.The small displacement pump powers the quadruple cylinder, the landing mast cylinder and the afterburner/lift cylinder.
2.Four outriggers
Small drilling equipment consists of hydraulic cylinders and fixed frames.The height of the body can be adjusted at the work site to support and stabilize the body.
3.Mast
A frame structure welded by giant steel pipes, channel steels and angle steels.The inner grooves of the channel steel on both sides are used as the power head to run up and down to ensure the verticality of the hole. The ups and downs of the mast are completed by hydraulic cylinders.
4.Power head
The mechanism with gear reducer has a large diameter mandrel in the middle of the low speed shaft.The upper end of the mandrel can be connected with the hose interface of the concrete pouring equipment to inject concrete; the lower end of the mandrel is connected to the drill rod and the drill bit through the blue plate. The high-speed shaft is driven by a high-torque hydraulic motor.
Rotary drilling rigs are often used for forward and reverse circulating mud washing rotary drilling rigs, that is, circulating mud washing rotary drilling rigs are composed of towers, drawworks, turntables, drilling tools, mud pumps, faucets and motors. engine. During operation, the power machine drives the turntable through the transmission, and the active drill rod drives the drill bit to rotate the broken rock layer at a speed of 30-90 rpm. The gas rotary drilling rig is an air compressor, not a mud pump on the rotary drilling rig, but uses compressed air instead of mud to clean the well. Usually, the reverse circulation method is also used, also known as gas lift reverse circulation. In other words, the compressed air is sent into the air-water mixing chamber in the well through the air supply pipe, and mixed with the water flow in the drill pipe to form an aerated water flow with a specific gravity less than 1. Under the action of the gravity around the drill pipe by the annular water column, the aerated water flowing in the drill pipe continuously rises and leaves the well, flows into the sedimentation tank, and the water after the sediment flows back into the well. The way of self-flowing. Using this type of drilling rig, when the well depth is very large (more than 50 meters), the chip removal capacity is greater than the pump displacement or the reverse circulation of the jet, so it is suitable for large drilling rigs with well water depth and water shortage areas, as well as freezing in freezing areas Floor.
Where are air compressors commonly used in the drilling industry?
1. Formation and Debris Removal
During the drilling process, an air compressor is utilized to create high-pressure air that is forced down the drill pipe. This pressurized air is crucial for two main purposes – formation and debris removal. As the drill bit advances into the ground, the high-pressure air blows away the drill cuttings and helps clear the wellbore. This ensures that the drill bit can continue to penetrate the formation effectively and prevents the accumulation of debris that could hinder the drilling progress.
2. Cooling and Lubrication
Drilling operations generate substantial heat due to the friction between the drill bit and the formation. Air compressors play a vital role in cooling and lubricating the drill bit and the drill string. The compressed air is directed to the drilling tools, providing a continuous flow of cool air to dissipate the heat. This cooling effect helps prolong the lifespan of the drilling equipment and reduces the risk of premature wear and damage.
3. Hammer Drilling
In water well drilling, a technique called hammer drilling is commonly used. This method involves using compressed air to power down-the-hole (DTH) hammers, which deliver impact energy to the drill bit for efficient rock penetration. The air compressor supplies the necessary compressed air to drive the hammer, delivering powerful blows to break the rock formation. This technique is highly effective in hard rock drilling and enables faster and more efficient drilling progress.
4. Well Development and Cleaning
After drilling is complete, the newly constructed well requires thorough development and cleaning. Air compressors play a crucial role in this process as well. Compressed air is used to blow out any remaining debris, sediment, or fine particles from the wellbore and the surrounding formation. This ensures that the well is clean and free from obstructions, allowing for efficient water flow and preventing potential issues such as clogging or reduced well yield.