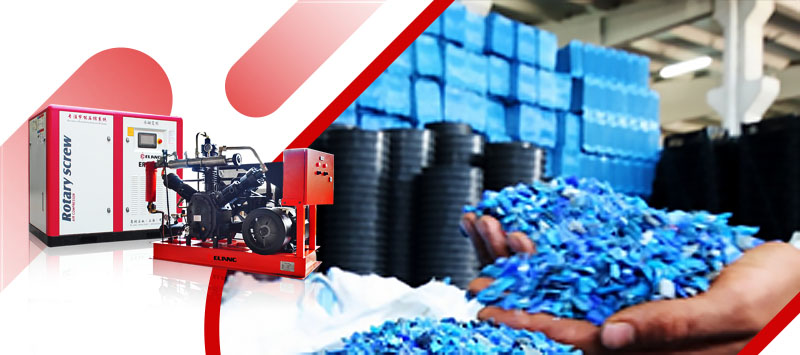
As the power source of compressed air, air compressor is widely used in the national economy. There are small piston air compressors, medical silent oil-free air compressors, integrated integrated air compressors, oil-free and water-free screw air compressors. This should be selected according to the compressed air requirements of the industry. The screw type air compressor is generally selected as the supporting air compressor for the injection molding machine.
The injection molding industry is a relatively large industry in the national economy, such as toy molds, footwear molds, container molds, plastic wood molds, tube embryo molds, aviation molds, rotational molding molds, clothing molds, automobile and motorcycle molds, agricultural tool molds, etc. these industries need to be applied to air compressors.
How is the air compressor used in the injection molding industry?
Air occupies a certain space, but it has no fixed shape and volume. When pressure is applied to the air in the closed container, the volume of the air is compressed and the internal pressure is increased. When the external force is withdrawn, the air will return to its original volume under the action of the internal pressure. If there is a movable object in the container, when the air returns to its original volume, the object will be pushed out by the pressure of the air in the container. This principle is widely used in production and life.
1. Mold Cooling
Injection molds need to be cooled to solidify the molten plastic material quickly and ensure efficient production cycles. Air compressors supply compressed air to cooling channels within the mold, expelling heat and facilitating faster cooling. This helps maintain the structural integrity of the molded parts and enables shorter production cycles.
2. Ejector System
After the plastic part is molded and cooled, it needs to be ejected from the mold cavity. Air compressors are often used to power the ejector pins, which push the part out of the mold. Compressed air creates the force required for a smooth ejection process.
3. Pneumatic Actuators
Injection molding machines often incorporate pneumatic actuators to control various movements, such as opening and closing the mold, moving core slides, or operating robot arms. These actuators utilize compressed air to generate the necessary force for these movements.
4. Part Cleaning and Drying
Before assembly or packaging, molded parts may require cleaning or drying to remove any contaminants or moisture. Air compressors are used to supply compressed air for blowing off debris, dust, or water droplets from the parts, ensuring their cleanliness and quality.
5. Material Conveying
In large-scale injection molding operations, raw plastic material is typically stored in bulk containers or silos. Compressed air is used to convey the material from the storage containers to the molding machine’s hopper, enabling an efficient and automated material feeding system.
6. Instrumentation and Control
Air compressors may also be used in the instrumentation and control systems of injection molding machines. For example, compressed air is employed in pneumatic controls, sensors, and valves, contributing to the overall automation and functionality of the equipment.
In the injection molding process, there is another technology that can make the role of compressed air very important. That is air assisted injection molding technology. Basically all thermoplastics used for injection molding and general engineering materials (such as PS, hips, PP, ABS…) are applicable to air assisted technology. At present, air assisted technology is widely used in various plastic products, such as TV sets, refrigerators, air-conditioning or audio enclosures, automobile plastic products, household appliances, daily necessities, toys, etc.